14 October 2023
Clothes need recycling? Sorted
Philip Halcrow
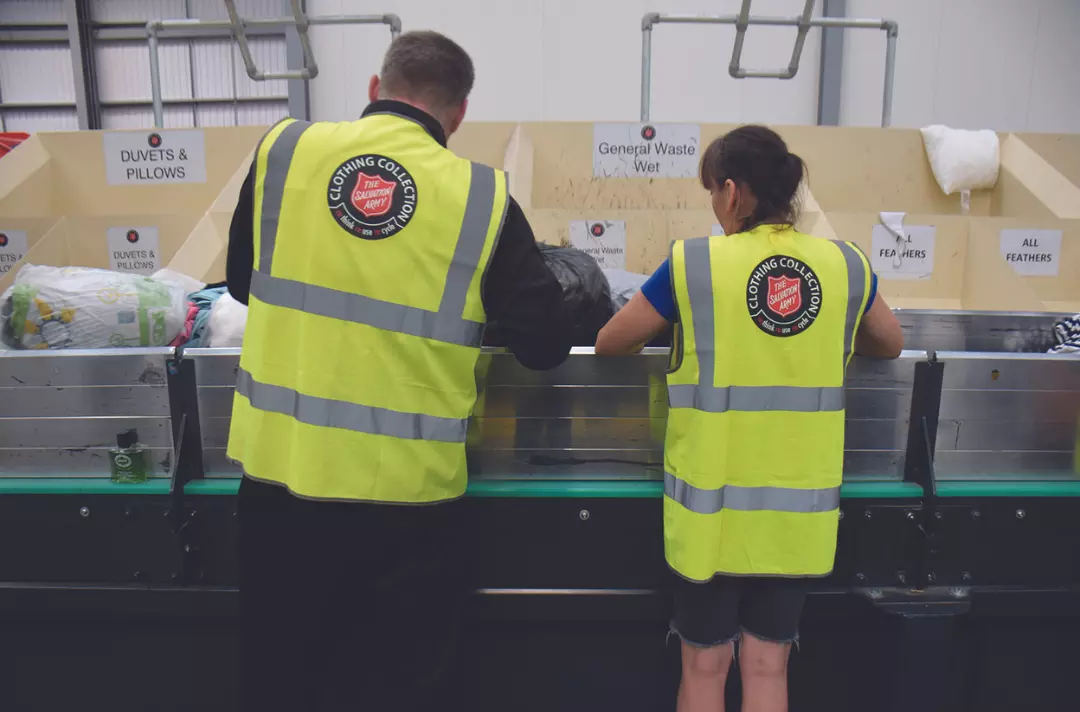
War Cry's Philip Halcrow visits a Salvation Army Trading Company (SATCoL) facility in Kettering to find out more about their textile recycling process.
- SATCoL's recycling centre is featured on Songs of Praise (18 February 2024).
At any one time there are some 250 vehicles on the road, gathering textiles from The Salvation Army’s thousands of clothing banks across the UK and delivering them to facilities where – along with other goods – they will be processed for reuse and recycled, bringing material benefits to the planet and people.
Every few seconds the machine produces a burst of air and fires an item of clothing from the conveyor belt into one of the bins below. John Webb, the site manager for the Salvation Army facility in Kettering, explains how the technology next to us is helping the textile recycling process.
‘There are two cameras,’ he says. ‘One recognises colour and the other is a spectrometer that picks up the wavelengths of the clothing – polyester, for instance, will give off a different wavelength from cotton. The cameras and the computer work together to translate that into something we can see.’
The composition and colour of the fabric are displayed on a screen and then, at the right moment on the item’s journey down the conveyor belt, a jet of air sends it into the appropriate bin.
‘So we can see,’ says John, indicating the screen, ‘that the last product that went through will have gone into the bin for low-grade cotton polyester, the blended grades.’
The Fibersort technology is assisting SATCoL – The Salvation Army’s trading arm – in its efforts to find more and more ways of using everything possible that is donated through its clothing collection schemes.
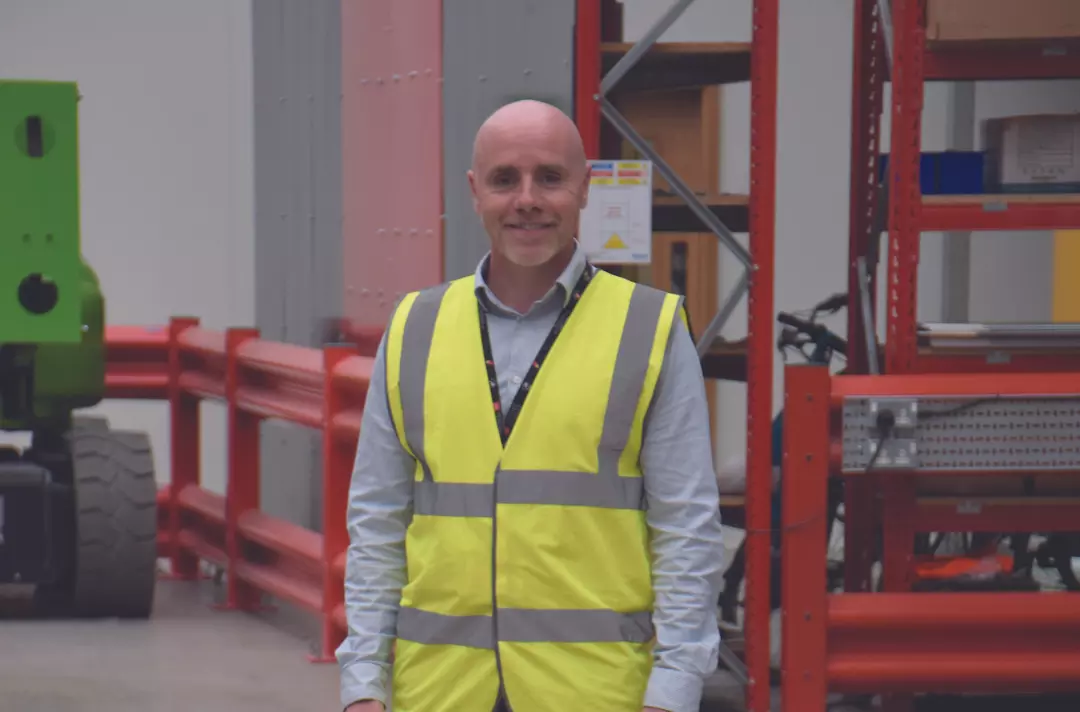
The best-quality clothing that arrives at the facility may be creamed off to be sold in The Salvation Army’s hundreds of charity shops – though, because of direct donations, they are rarely in need of extra stock. The rest of the 60,000-plus tonnes of textiles collected by SATCoL each year ends up in a variety of guises at home and abroad.
‘Our drivers are our first line of sorting,’ says John as we walk round to where vans are arriving to unload what they have picked up from some of The Salvation Army’s 8,000 clothing banks.
‘Part of our deal with placing our clothing banks at supermarkets is that we remove anything in and around our banks. It could be glass bottles, cardboard, fridges, freezers. We work with supermarkets and police to deter fly-tipping.
‘Once a driver gets to a clothing bank, if they see a bag that isn’t clothing, they still pick it up. If it’s just books, they keep that to one side and we put them into tote boxes. A company buys them off us. They can put them through a conveyor belt system that scans the barcodes and automatically uploads them to online platforms where they can be sold.
‘Our goal is to do everything we can to ensure nothing goes to landfill. At the very worst it will go to waste that is incinerated for energy. The waste we pick up may not be what we would have liked, but we want to have done the right thing with it.’
Books and the like set aside, the textiles are emptied on to a conveyor belt, either manually from the vans that have been out on collection rounds nearby or automatically from one of the giant trailers strategically placed in secure locations around the country. The trailers are filled with collections by drivers on local runs until ready to be brought to Kettering.
‘The trailer is tilted about 48 degrees in the air, and gravity empties it out,’ says John. ‘We used to empty the trailers by hand, which would take three and a half hours. Now it takes about 30 minutes to tip 16 tonnes of clothes from a trailer – and within the hour they will be fully processed through the system and ready to go out to one of our customers.’
Unloaded, the donated textiles are sorted again by hand. Working on what is almost a reverse production line, a team sift out duvets and pillows, feathers, cardboard or general waste.
‘The main thing we probably get that fills up the chutes is duvets,’ says John. ‘They’re not something we ask for, but we don’t like to say no. If you say no to something, you may not get the bits you do want. And we have an outlet for them.’ The textiles are then given another manual sort.
‘Unwearables – that is, anything that’s worn, torn or looking as if it’s at the end of its life – are put down a chute, and they go over to the Fibersort area.’ Many of the wearable items of clothing are exported and sold by the tonne to customers from all over the world.
John explains: ‘We’re averaging 40 to 50 loads a week out of here or our other site at Winchester, and that could be anywhere from Hungary to Dubai. We sell to customers that will do a thorough sort on the contents of the bags for different markets throughout the world. For instance, we have a customer in Hungary that will take our stock, supply their shops with what they require and then sort the rest for other markets.
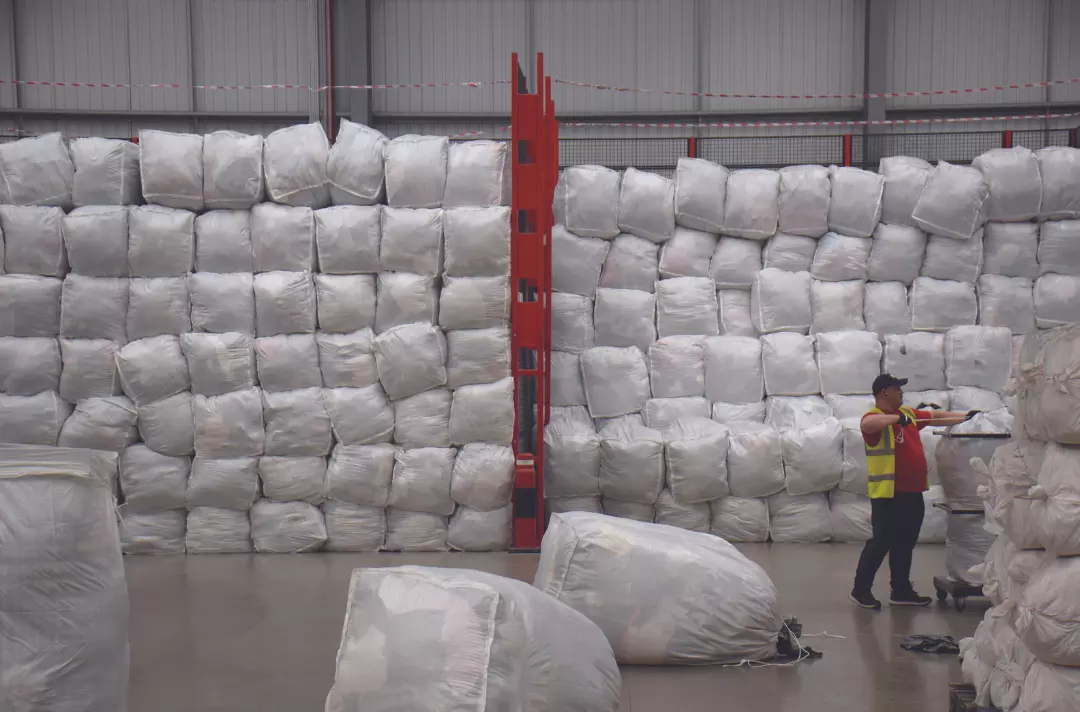
‘With our Fibersort system, we’re trying to remove unwearables from what goes into the bags, rather than just giving them everything.’ Fibersort is helping in other ways – and its possibilities are still being explored. ‘We’ve had this machine a year and a half, and we’ve been trying to find outlets for our waste to make it back into something useable,’ says John as he peers into the bin where textiles made up of 95 per cent cotton or above are accumulating.
‘This is unusable, unsellable end-of-life stock that our customers wouldn’t want. We have an outlet for this – a company in Sweden will take this, shred it, decolour the resulting slurry, then produce fibres for making into another item of clothing, maybe a T-shirt, blouse or dress. It will have gone from something waste to something brand new.’
Not every type of textile is so easy to recycle. ‘Nylon is a real headache. At first, we were sorting it, but nobody was doing anything with it – but that’s changing. BASF, the chemical company, have taken nylon and chemically turned it back into oil. Blended materials are being used for fillings in furniture. Necessity is the mother of invention, and we’re trying to find the clever people who have got ideas.’
One of the latest ideas being pursued by SATCoL is a groundbreaking machine capable of recycling polyester textiles back to their raw form.
John points out an old unusable, unsellable bedsheet and says: ‘The new machine will shred this and heat it up to liquidising point. Some filters will remove impurities. It will go through a cooling process and will come out as little pellets of recycled polyester, which can then be respun into new clothing or turned into something else.’
In a meeting room behind the scenes, Bernie Thomas, circular economy and sustainability manager, describes SATCoL’s polyester recycling scheme – labelled Project Re:claim – as a ‘world innovation’.
He says: ‘We’ve been given funding from the Department of Energy Security and Net Zero to cover some of the cost, because nobody has tried this before. We’re the first commercial operation to do this and return those materials back into clothing and other textiles, rather than forgetting about them.
‘At present, most of the recycled content in clothing is coming from plastic bottles, which are not being recycled back into plastic bottles. Retailers and brands are setting themselves targets – they’d like to include more recycled content in their clothing, so we’re hoping this project will contribute some of the materials to that. It’s the right thing to do, rather than waste these finite materials.’
SATCoL works to prolong the lives of goods other than textiles. ‘By volume, the materials we collect are predominantly textiles, but in our charity shops we’re collecting, reusing and repurposing all kinds of products – such as household goods and furniture – and selling them, extending their lives,’ says Bernie.
SATCoL has also formed a partnership with home appliance manufacturer Beko that will enable people to buy spares for existing items rather than have to replace them. Beko will supply SATCoL with goods returned by customers.
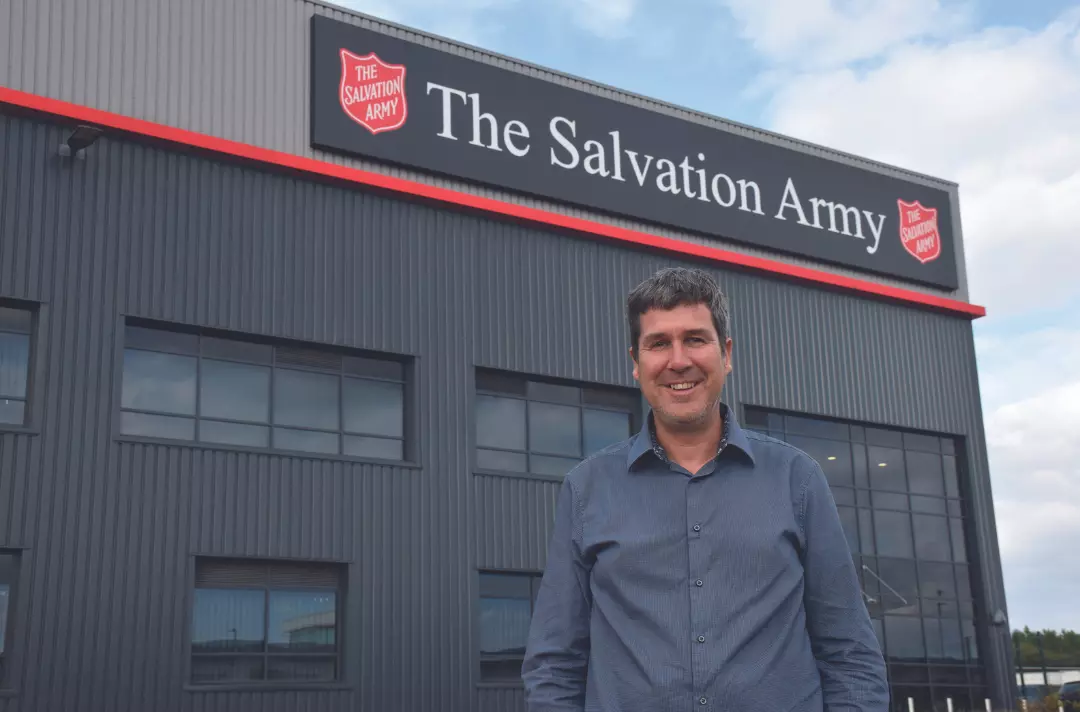
‘We are creating a bit of a parts farm,’ says John. ‘So, if you buy a coffee percolator and you break the jug, you will be able to come to us online and buy a new jug for that percolator rather than have to buy a whole new appliance – because companies like Beko don’t necessarily sell just the spares.’
SATCoL also takes laptops from schools or businesses that are in the process of replacing them, wipes the data from them and sells them in its shops at a price well below that of a brand-new model.
As with all its work, the money made goes towards supporting the work of The Salvation Army in communities across the UK – work which SATCoL assists in other ways, for instance by supplying shoes and coats to the Every Child Warm initiative run by the Salvation Army church in Gateshead and clothing to a scheme for asylum-seekers in Glasgow.
Bernie says that he appreciates the fact that The Salvation Army’s values chime with his own. ‘I feel that they’re an excellent fit for me in terms of purpose, which I guess comes from my Christian belief system around doing the right thing. Our work is all about doing something useful, looking after the environment and looking after people.’
- For more information, visit satcol.org.
Written by
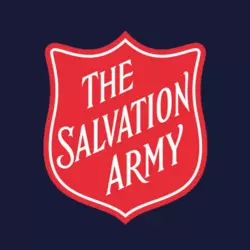
Philip Halcrow
Deputy Editor, War Cry
Discover more
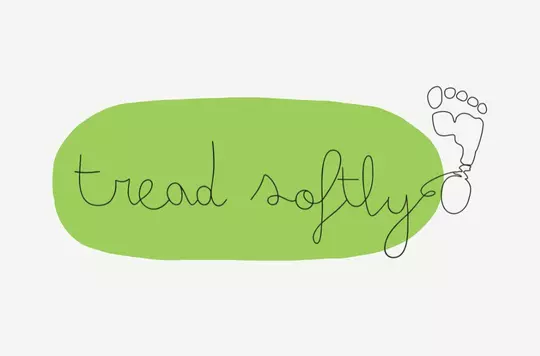
Supporting the territory to care for creation and tread softly on our common home.
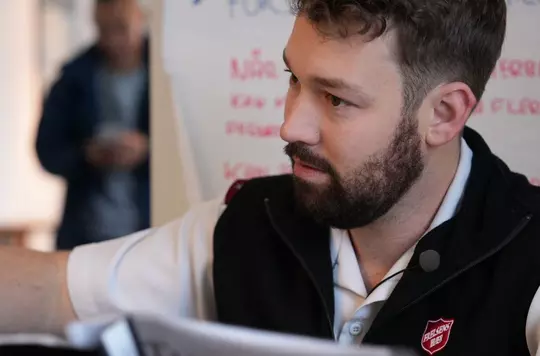
Captain Nathanael Münch shares his experience as a corps officer in Greenland for the 2024 Self-Denial Appeal.